Enhanced safety & cleaner output
Our sustainable recycling process extracts raw materials from end-of-life batteries. This ensures a circular solution as secondary raw materials are reintroduced into the manufacturing of new batteries, making them much greener than batteries produced from primary raw materials.
We collect lithium-ion batteries from electrical vehicles and industrial batteries ourselves and in collaboration with scrapyards or partners. These batteries are usually end-of-life, recalls, or R&D, in which need to be recycled and transported safely to the nearby facility.
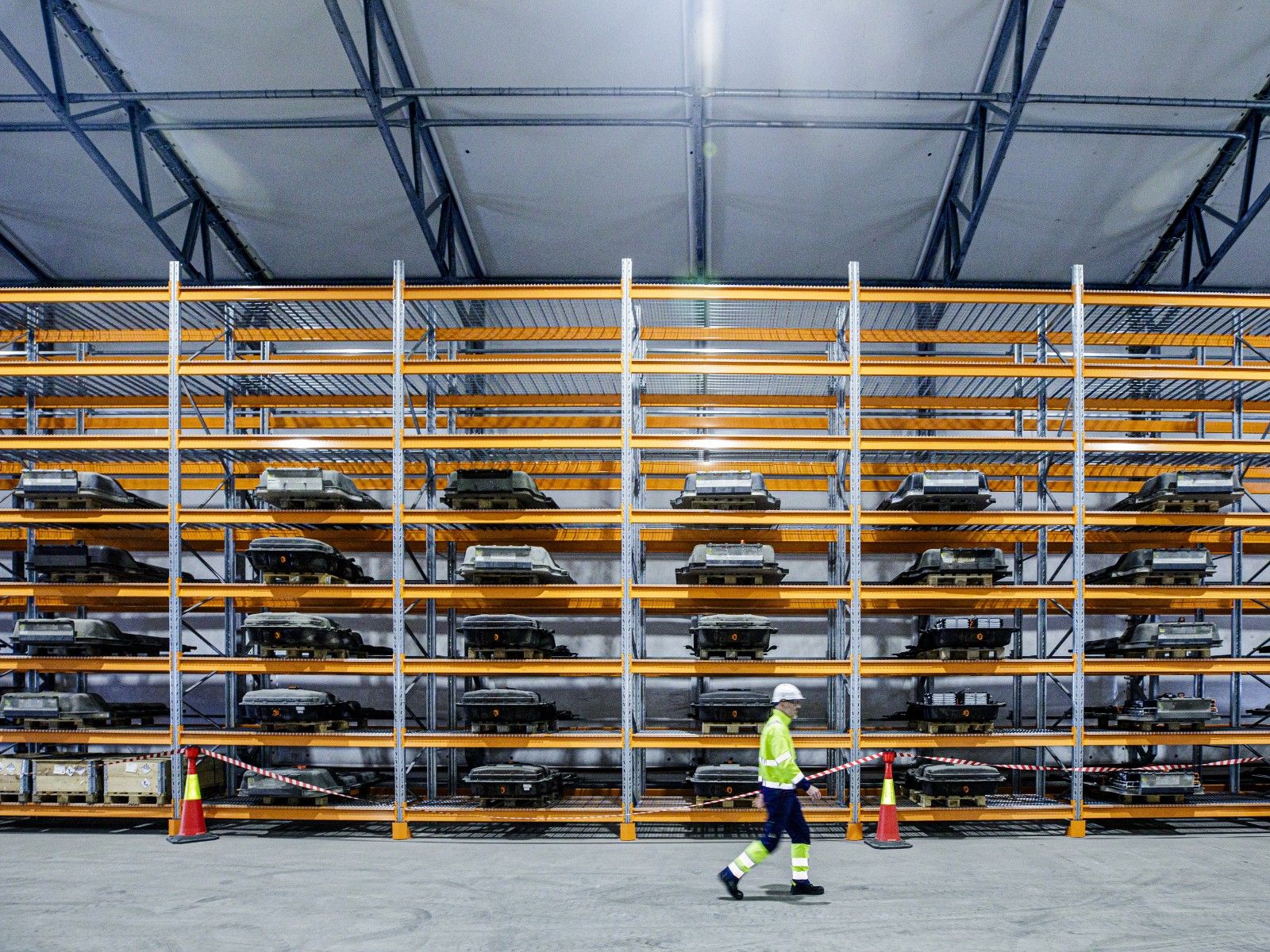
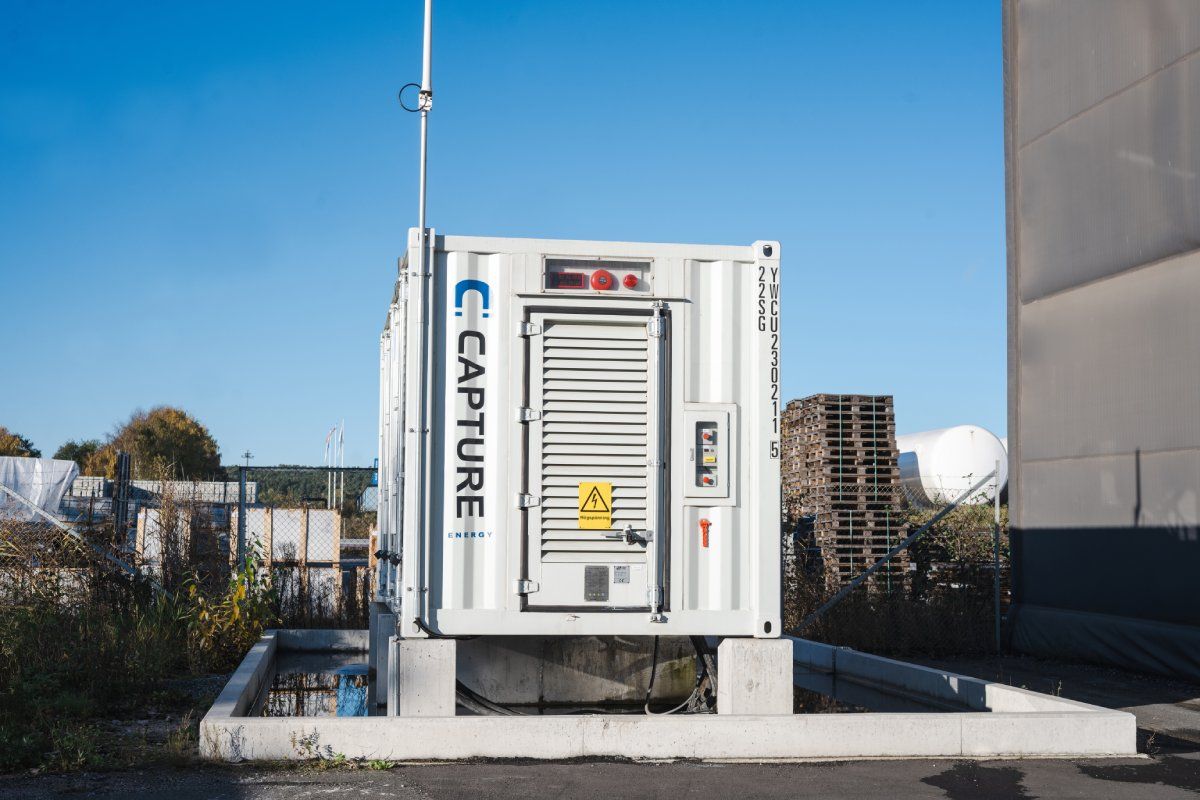
After diagnosis and preparation, the batteries are discharged to remove the residual energy. We usually spend about 2 hours discharging the battery to 0 volts to ensure the battery is dead and ready to be safely handled upon dismantling and crushing.
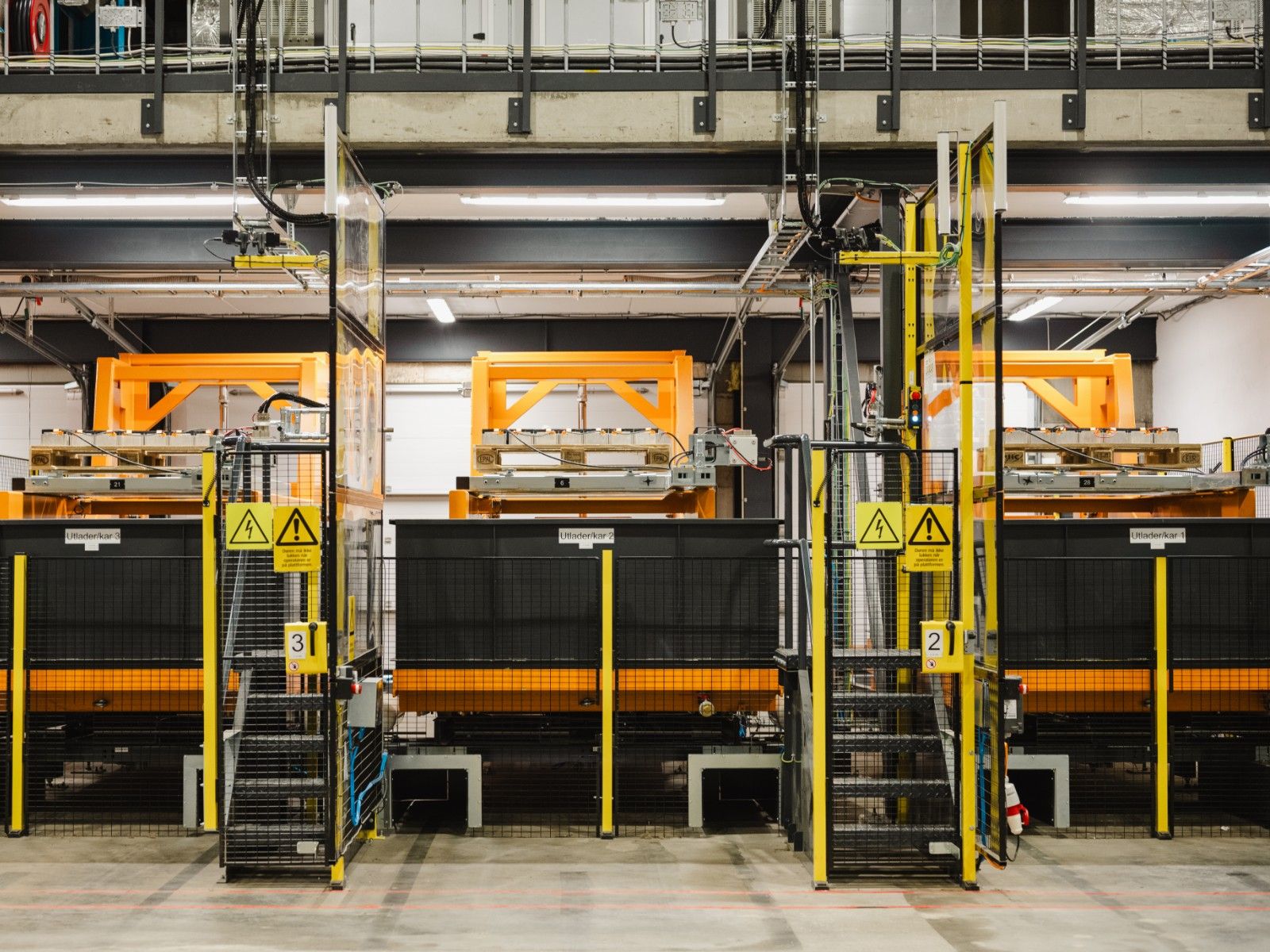
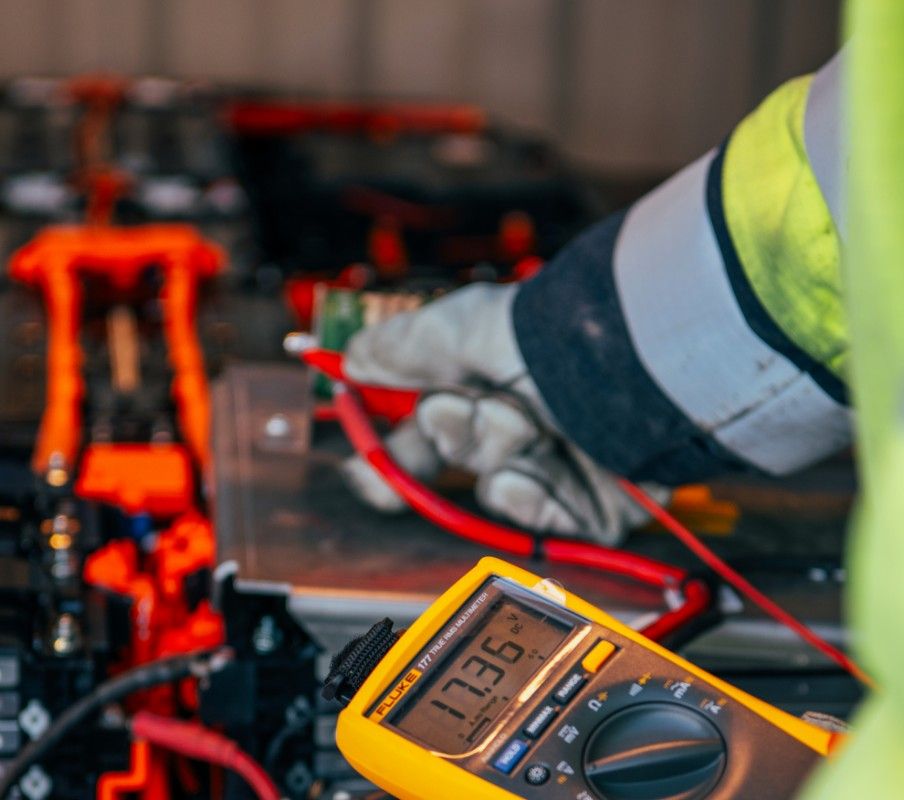
The second discharge step is the deep discharge. The deep discharge is performed using resistors, to ensure that the battery is at O.O voltage as the batteries may have a small voltage increase upon disconnection from the battery load unit due to the recovery effect. This step is therefore a must follow.
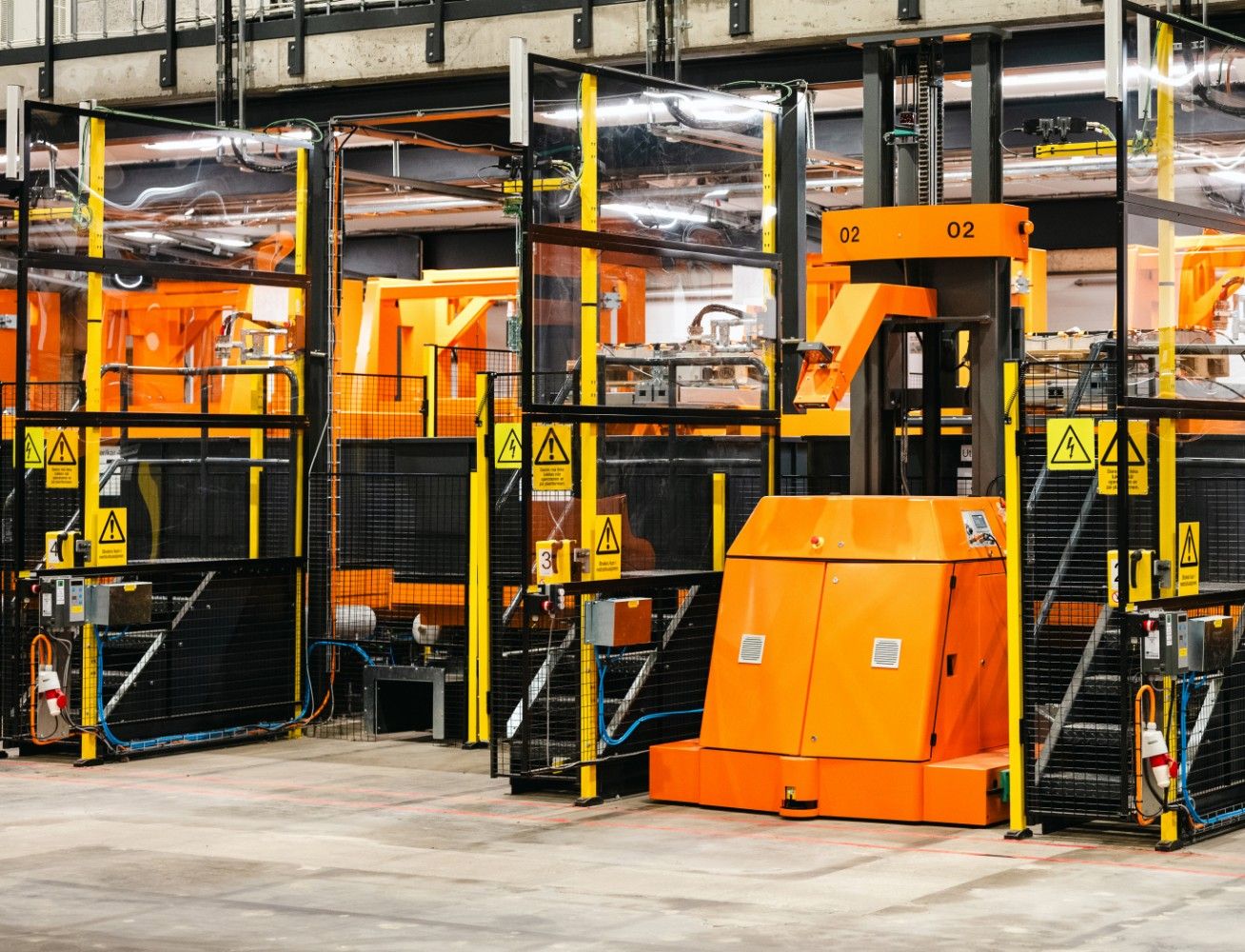
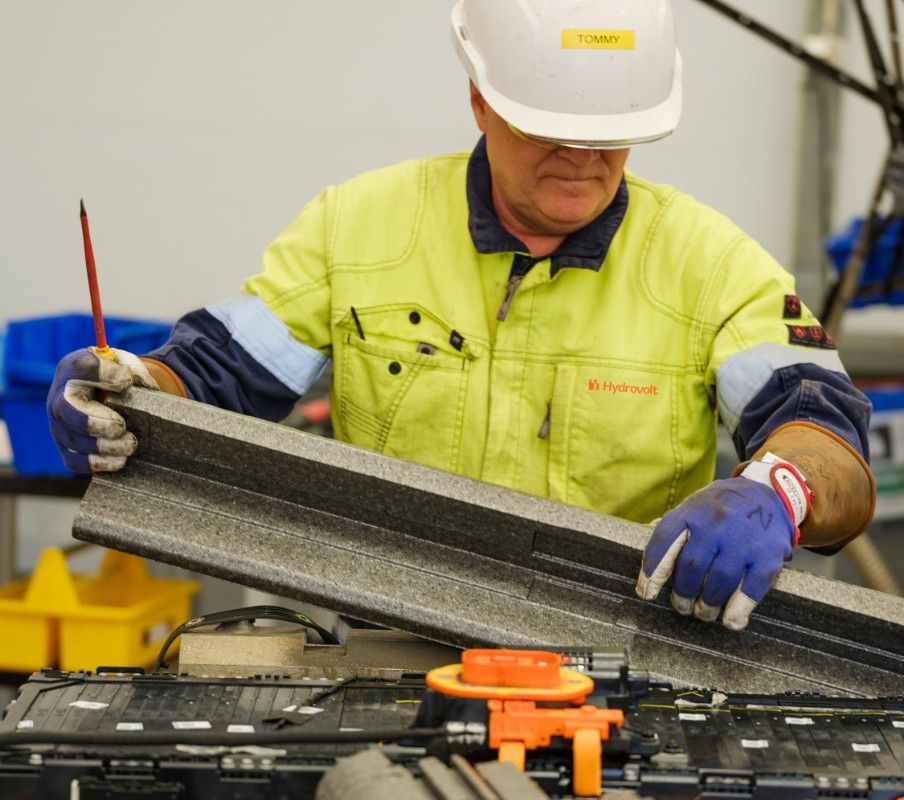
After the discharge step, the battery pack is considered safe to dismantle and transported with the AGV to the dismantling stations. Dismantling is performed manually using power assisted tools, and all components such as cable harnesses, frames, plastics, fasteners are also removed from the assembly and collected in separated containers for recycling. Battery modules are now clean and ready to be transported for crushing and sorting.
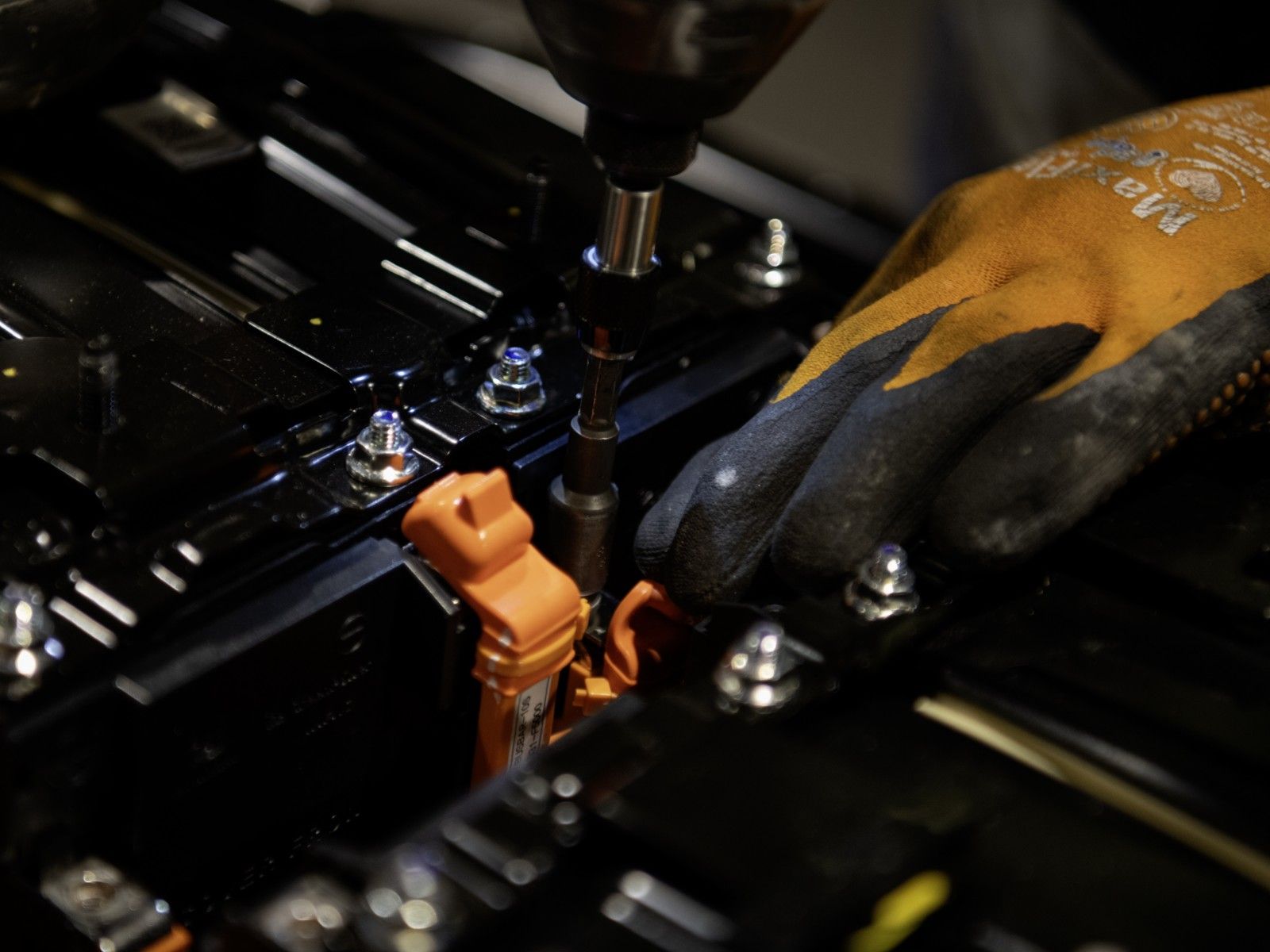
From the infeed lock, battery modules are fed into the first crusher and the material is further processed to the second crusher. Both crushers are constantly flushed with inert nitrogen gas during operation to avoid fire. From the crushing stage, the crushed battery material is transported to the drying stage to separate solid materials from liquids.

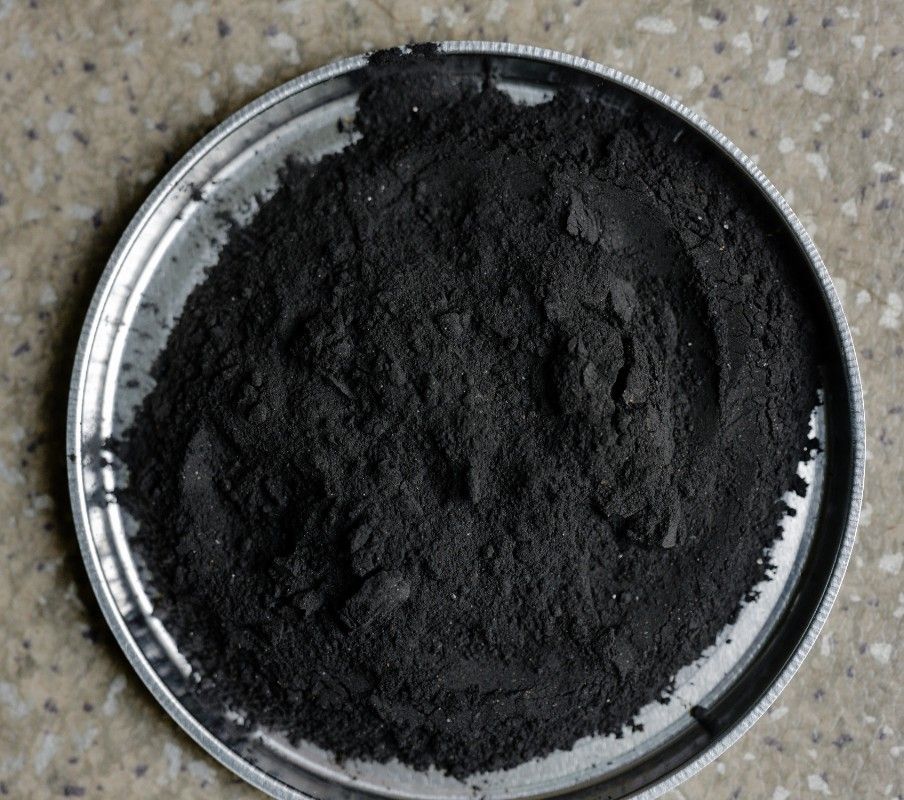
The solid fraction is sorted by various mechanisms and at the end of the sorting stage, a number of material fractions can be collected.
recovery rates
fractions
critical raw materials in black mass
energy recovery from collected batteries
Carbon footprint of extracting critical battery materials by conventional mining vs. producing critical battery materials by recycling
A life cycle assessment has been carried out to calculate the carbon footprint of our operations. Using a cradle-to-gate approach, where the cradle is defined at the beginning of the collection process and the gate defined after the C&S process, before the black mass is sold to offtakers.
The result concludes on a very low carbon footprint of less than 0,2 kg CO2 per kg black mass, proving it is possible to develop greener batteries through recycling and the use of secondary raw materials in new batteries.
With lower environmental footprint, recycling is a more sustainable alternative to conventional mining. The assessment shows that we have a 75% lower carbon footprint compared to extracting materials by conventional mining.
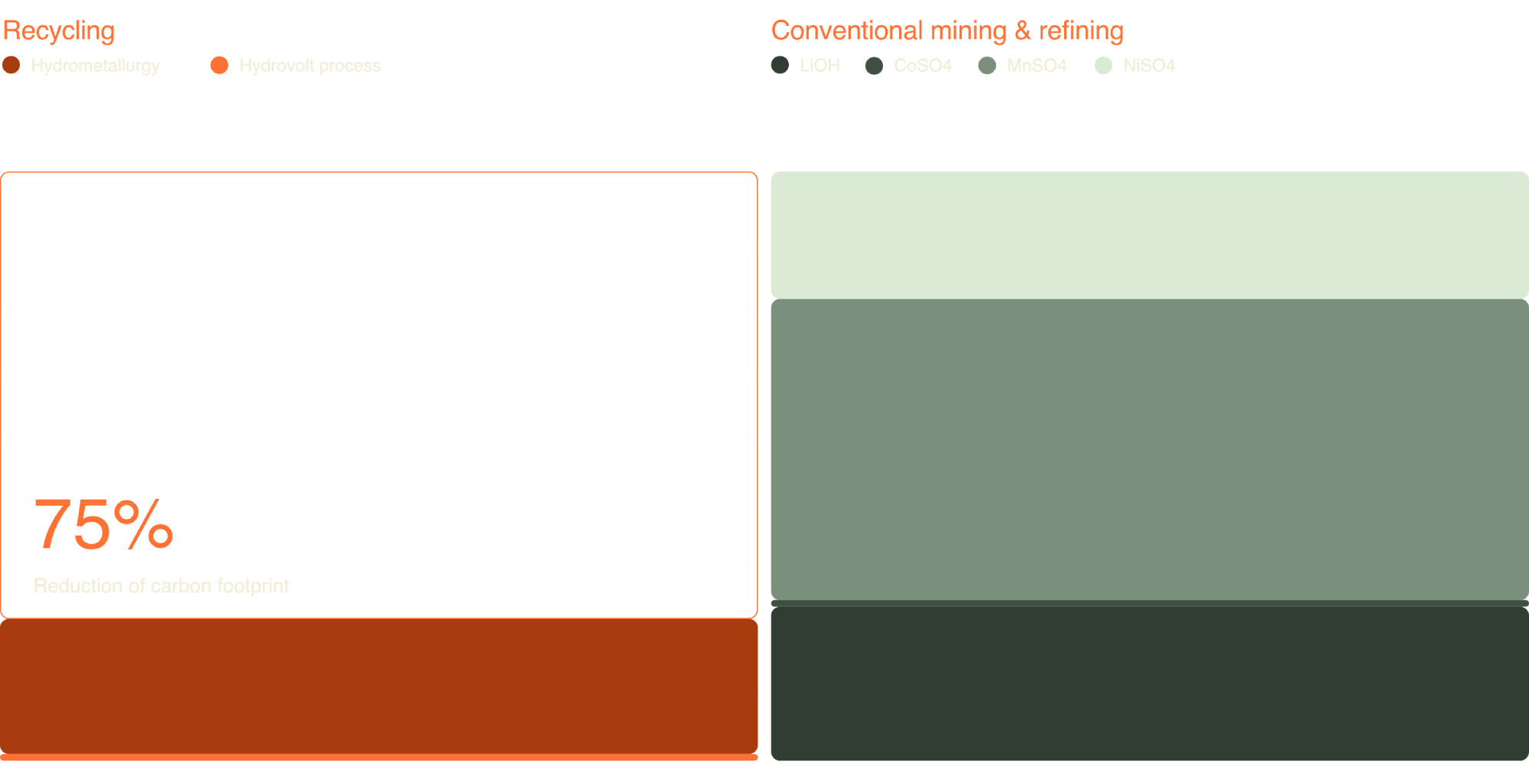
Full transparency
We innovate to ensure full transparency and traceability of the batteries through our recycling process.
Less transportation
We ensure easier logistics and reduced environmental impact as we aim to operate locally.
Market pioneers
Running one of Europe’s largest battery recycling plants since 2022, making us one of the leading actors in the market.
Smaller footprint
Our black mass has 75% lower carbon footprint compared to conventional mining.
100% materials back
We aim for the highest recovery rates in the battery market and work our way up to a 100%.
Safer & cleaner
Our unique automated D&D and dry-environment process offer enhanced safety and cleaner output.